2023 Charged Up
Velociraptor
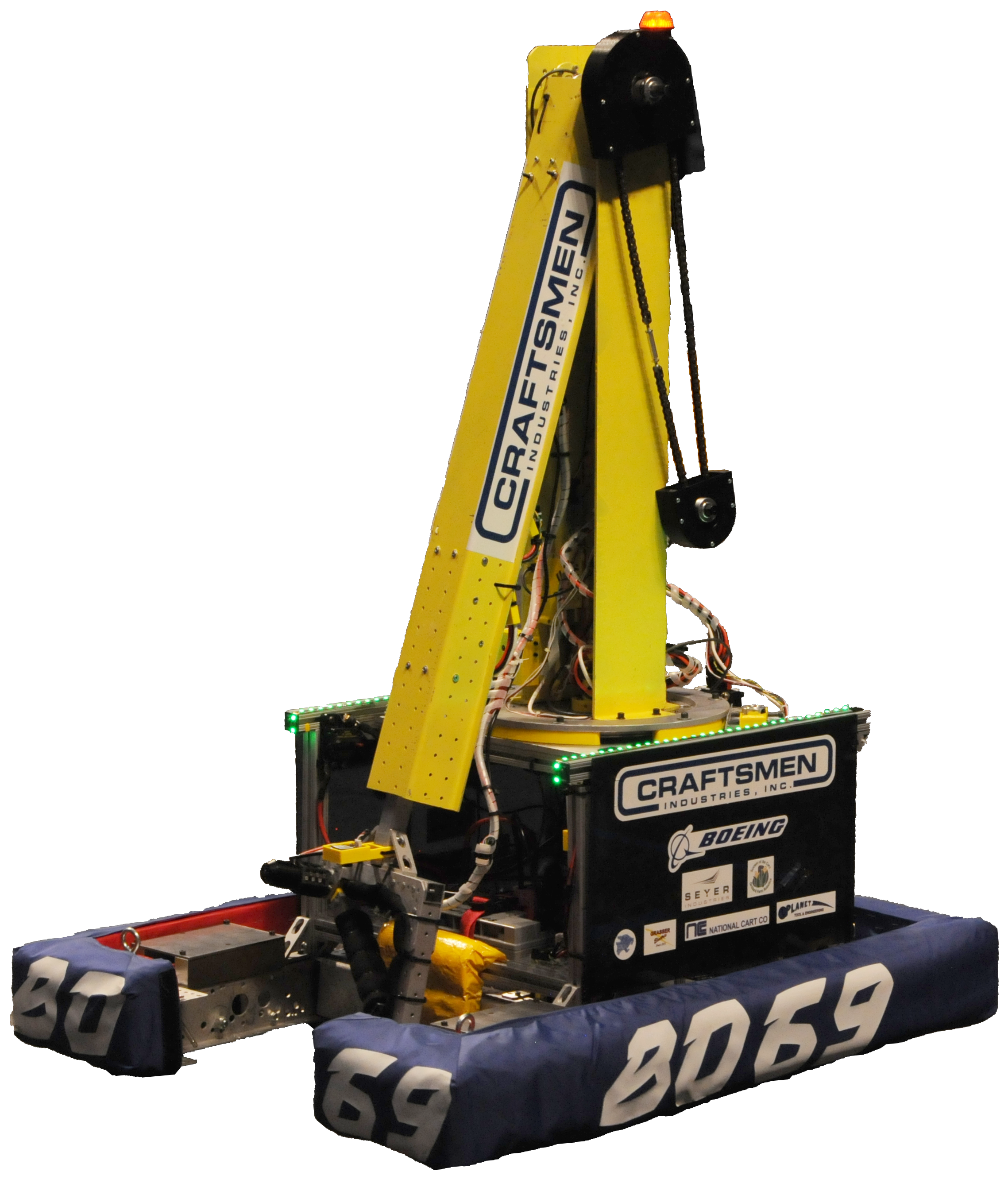
The Velociraptor was built in 8 weeks from the first week of January to early March of 2023. The team had 11 students, more than doubling in size from the previous year. In the St. Louis Regional, we placed 31st out of 43 teams. Although we did not rank as high as we had hoped, we learned valuable lessons for future seasons.
Game Description
In the 2023 challenge, CHARGED UP, the time period consisted of a 15 second autonomous period, and then 2 minutes and 15 seconds of teleoperated (Human controlled) period, including the final 30 seconds, referred to as Endgame. There were two main goals for the 2023 challenge: place the game pieces onto the nodes and dock / engage with the charge station. Whichever alliance had the most points at the end won.
Drivetrain
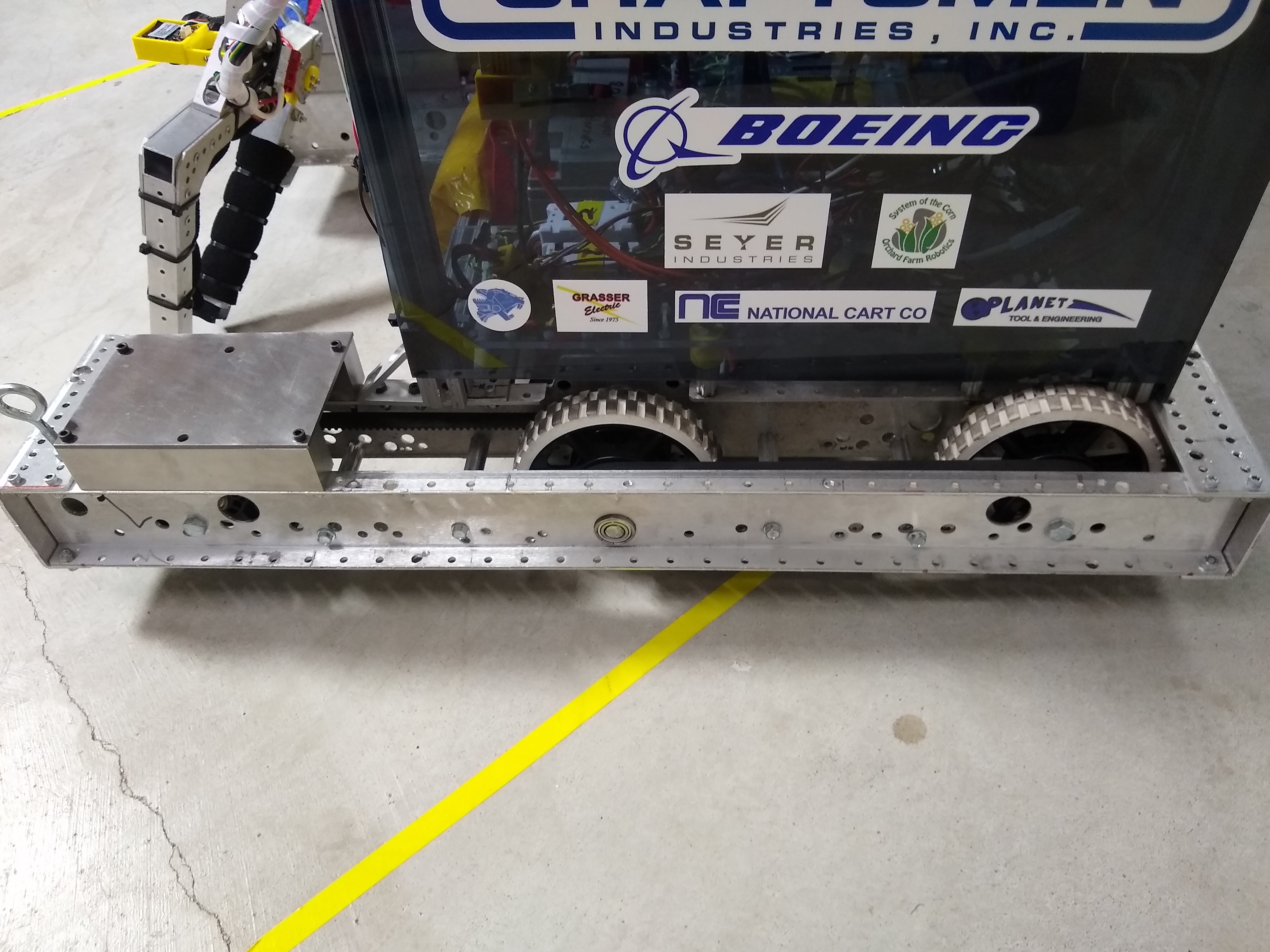
This season, we decided to go with a 6-wheel drop-center tank drivetrain.The reason for it was because we wanted to have enough torque to be able to climb on top of a lexan-covered ramp inclined at an 11-degree angle. Doing so would allow us to score more points during each match. To achieve the amount of torque required to drive a 100+ lb robot up the ramp, we used 4 brushless 12V motors driving two toughbox mini gearboxes geared with a 8.45:1 ratio, giving us the desired amount of torque to meet our needs while still retaining a very significant amount of speed.
Turntable
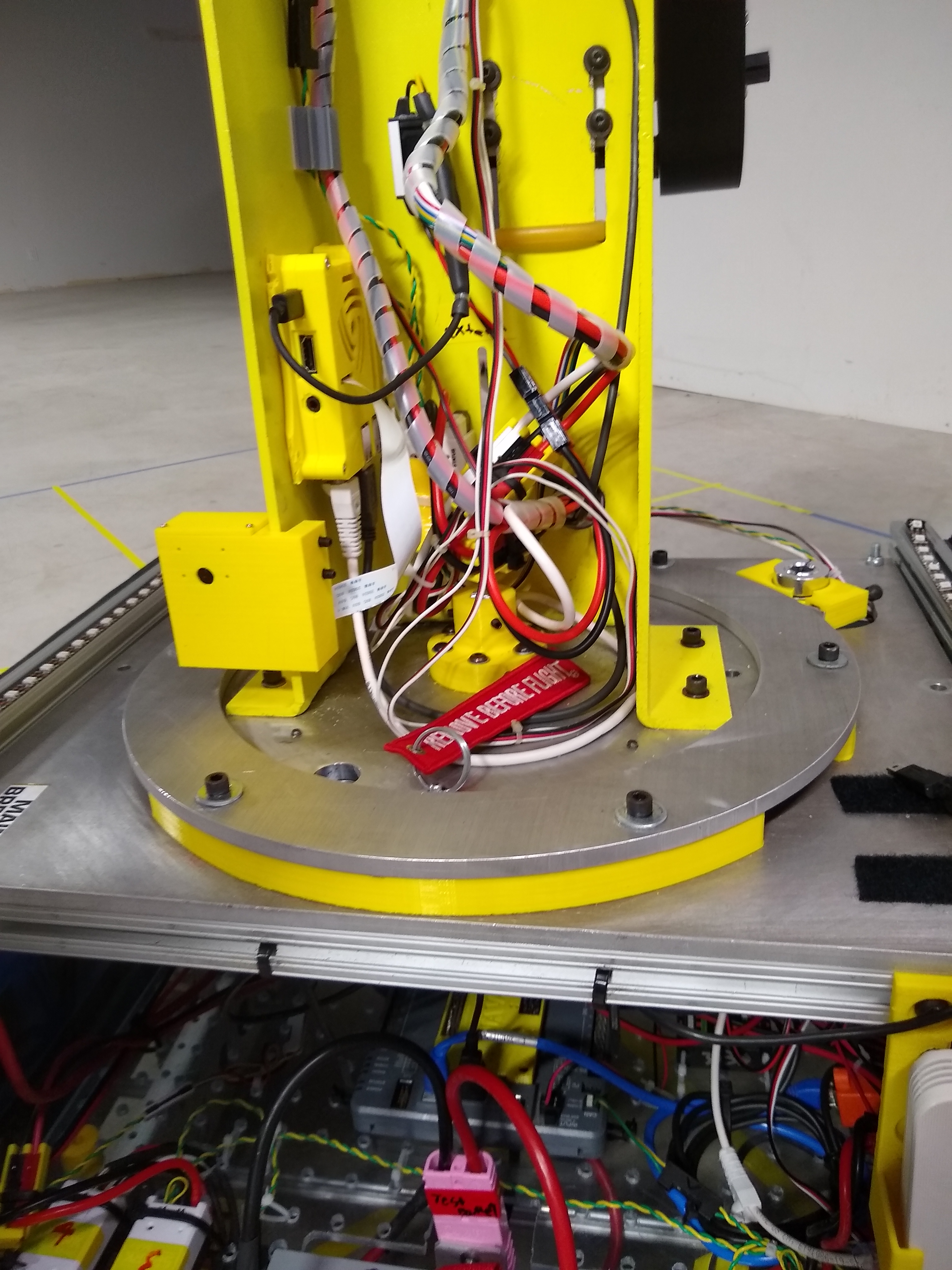
The turntable was designed so that the arm could be rotated horizontally. It was especially useful because we used tank drive, so the turntable enabled the robot to adjust its angle of picking and placing without rotating the entire robot. Originally we wanted to use it to pick up from behind the robot, but the way we designed it meant that it would have been difficult to route the wires to be able to handle so much rotation. It ended up being able to rotate around 135 degrees in each direction from the front. However, in competition we mostly used it for minor rotation from the front to place game pieces. The mechanism was chain driven by a Neo motor with a 60:1 gear ratio. It rotated on a Lazy Susan, which was sandwiched with a tiny gap between two aluminum pieces machined by Seyer Industries in order to protect the Lazy Susan itself.
Arm
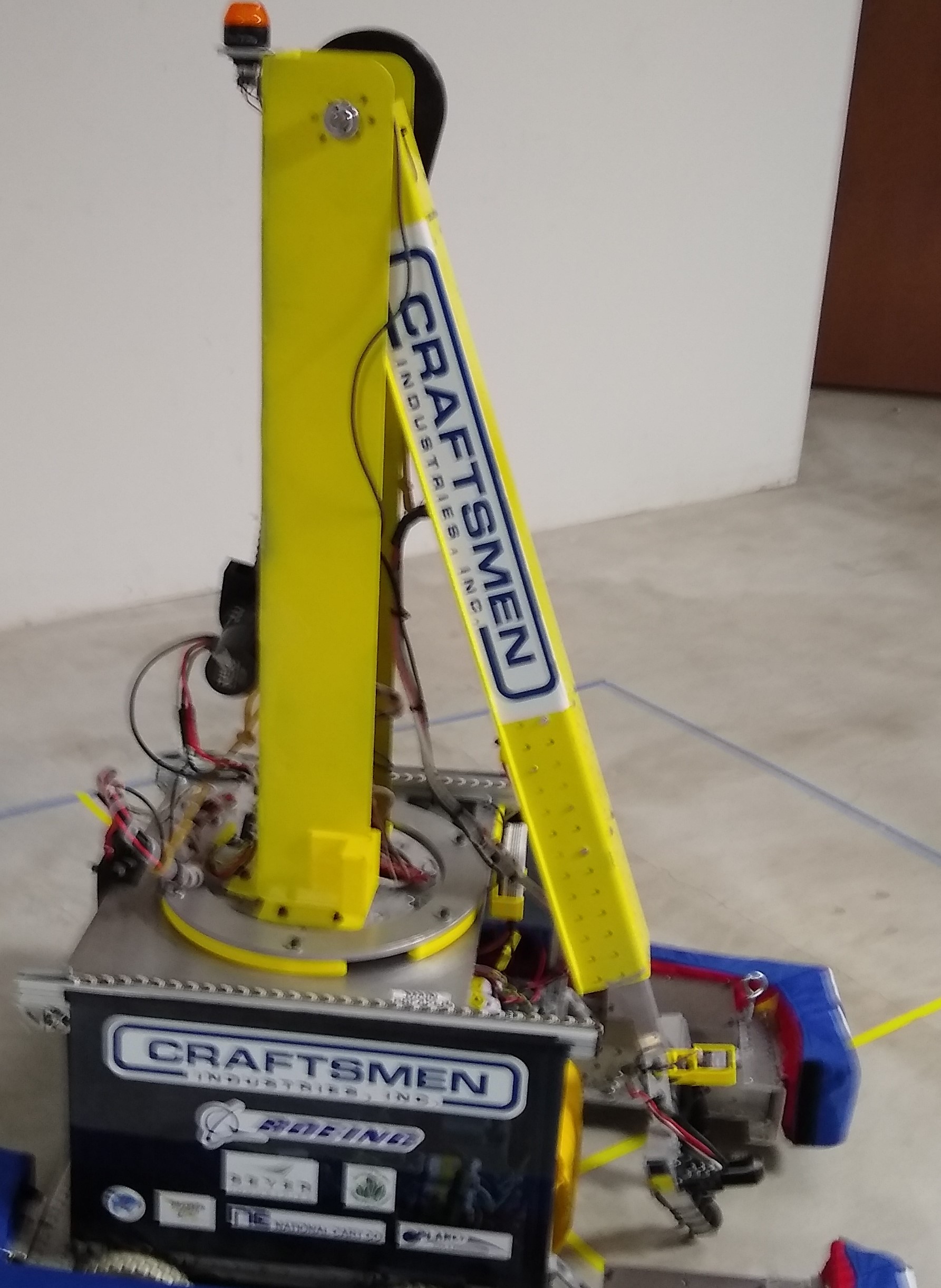
The arm, a major component of the robot, rested on a rotating turntable and could extend out to reach the highest nodes. The vertical movement was chain driven by a neo motor with a 60:1 gearbox and a 3:1 additional gearing from the sprockets we used. As we were talking about designs, we quickly realized that to get to the highest nodes we would have to extend. We thought about many options such as repurposing a climber extension or using a scissor mechanism, but ended up deciding on a lead screw to power it. The structure of the arm itself was made of aluminum custom machined for us by Seyer Industries. Though many parts of our robot broke, this was one of the most consistent and reliable parts of our robot, and we had minimal issues with the main portion of it (excluding the extension mechanism).
Grabber
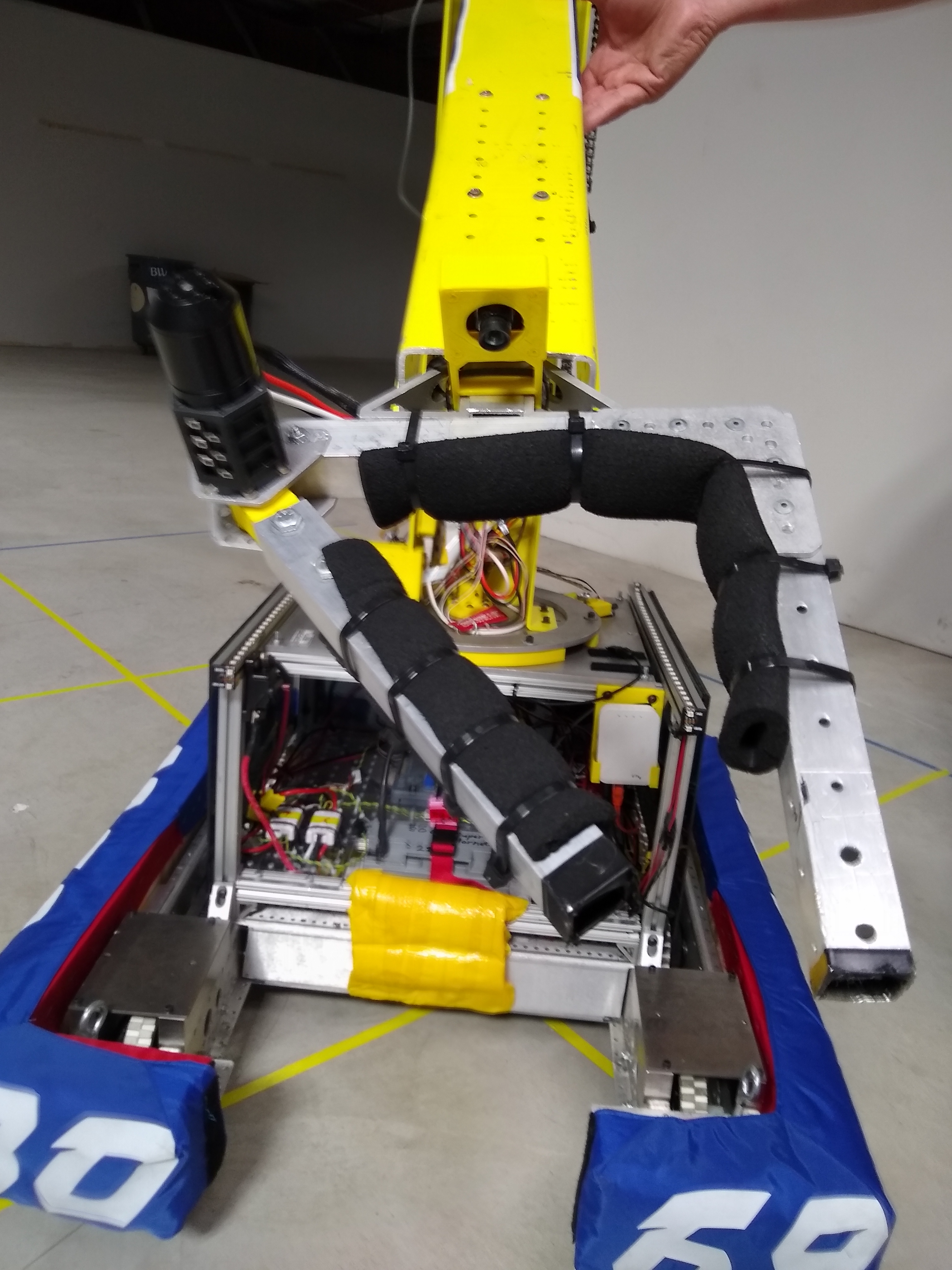
Software/Electronics
For the 2023 season, we made several improvements to our programming and electronics. We used newer motor controllers, which enabled us to use position and velocity controls for our motors. That made autonomous easier to program, because we could use distances to control the path of the robot. We also added cameras this year. We displayed the camera feed on the driver station, and we used it for vision based driving. There were targets on the field that the camera could recognize, which we used to find our position. We used them for tracking distances in auto mode and for lining up to place game pieces.